Terminology associated with ear impression material is sometimes confusing to those who take ear impressions on a routine basis. This post continues the discussion on ear impression terms from a previous post.
Compression Set
This is the amount of permanent deformation resulting when a material is compressed to a specific deformation for a specified time and temperature. This test follows (ASTM D395) requirements for the material to be constantly compressed 25% (deformed) for a given period, and measured again after a 30-minute recovery time. Test times (22 to 1000 hrs) and temperatures (230C to 1500C) provide the test conditions. The value derived is the percent the sample fails to recover to its original configuration.
This is an important feature of ear impression material because the finished impression is often subjected to compression at certain times, often during shipping, and it is important that they recover to their original shape without distortion. This holds true for soft hearing aid earmolds, stock tips as used with RIC (receiver-in-canal) hearing aids and other types of compressible earplugs or ear buds.
Type of Cure
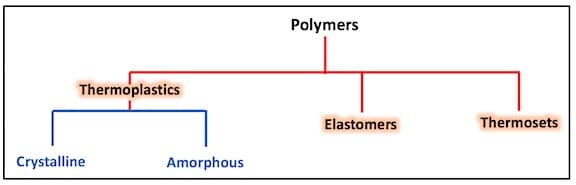
Figure 1. The most common way of classifying polymers is to separate them into three groups – thermoplastics, thermosets, and elastomers1. Ear impression material falls into the elastomer group.
Current ear impression material is a silicone elastomer (Figure 1), and classified as being irreversible, meaning that once it has set up, it cannot be reheated or other to reshape it. An elastomer is a rubbery polymer that can be stretched, but which rapidly returns to its original dimension when the applied stress is released. The setting-up or curing of the elastomer component mixture is the synthesis of polymers, and is referred to as polymerization.
For ear impressions, two types of silicone elastomers have been used primarily.
C-Silicone (condensation cure)
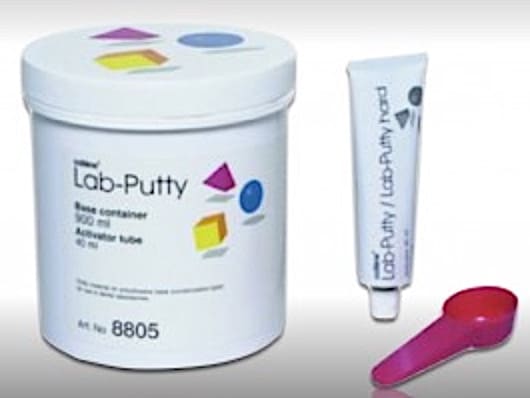
Figure 2. Condensation polymerization silicone consists of a base putty and a small volume catalyst.
Starting in about the mid 1960s, the C-type silicones (or what are also called condensation cured) found their way to ear impressions. This is a two-part alkoxy condensation cure. These used a cross-linking polycondensation reaction of hydroxyl terminated polysiloxane prepolymer with tetra alkoxy silanes catalyzed by dibutyl-tin dilaurate (DBTD)2. This involved a step-reaction intermolecular chemical reaction leading to the final “hardened” ear impression. What this means is that the process represents polymers having repeat units having fewer atoms than were present in the monomers from which they were formed (have a small by-product that is then eliminated). These have also been called room temperature vulcanizing silicones (RTV). These consist of a base putty and activator.
A problem with C-type silicones was that alcohol released (by-product) from the reaction mixture contributed to contraction/shrinkage of the impression. These were available with a base paste and a liquid catalyst (Figure 2). Condensation cure silicone is no longer used for serious ear impressions.
A-Silicone (addition cure)
Polyvinylsiloxane (PVS), or addition reaction/cure silicones were introduced in the 1970s, and found their way to ear impressions later in the 1980s These are supplied as a two-component 1:1 ratio system (Figure 3) consisting of a base paste and a catalyst3. Burgess3 describes the process where two monomers link to each other by an addition polymerization reaction, and no other small molecules are generated, as follows:
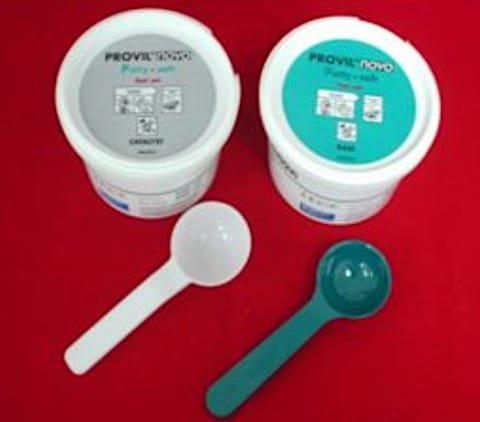
Figure 3. Addition polymerization silicone consists of 1:1 ratio system consisting of a paste and a catalyst.
The base paste contains a polydimethylsiloxand polymer in which some terminal methyl groups are replaced by silane groups, coloring, and silica filler. The catalyst paste contains a pre-polymer in which some terminal methyl groups are replaced by vinyl groups, a chloraplatinic acid catalyst, fillers, and colorants. When the two pastes are mixed, an addition reaction occurs between the silane and the vinyl groups, producing a cross-linked silicone rubber3.
What this means is that addition polymerization yields polymers with repeat units having identical molecular formulae to those of the monomers from which they are formed. To make this happen, a chemically active molecule (called an initiator) is needed to start what is called a chain reaction.
A-silicones have the advantages of being accurate, having the very lowest shrinkage among elastomers, providing good surface detail, being highly elastic, perfect elastic recovery, dimensionally stable, non-toxic, and non-irritant.
Contraction Ratio (Shrinkage)
All impression materials shrink after curing to some degree; however, addition silicone shrinkage is for all intents and purposes non-existent. In contrast, condensation cure silicone can have linear shrinkage of 0.5% over a 48-hour period of time. Both are significantly improved over previous ethyl methacrylate material that would shrink as much as 5-10%, making it difficult for the earmold lab to guess how much, and where to apply wax to compensate for the shrinkage and to allow a more comfortable fit4.
Polymerization
Polymerization is the method of creating a synthetic polymer by combining many small monomer molecules into a chain held together by covalent bonds. There are two main forms of polymerization, step growth and chain growth. The primary difference between the two is that in chain growth polymerization, monomer molecules are added to the chain one at a time (addition cure), whereas in step growth polymerization, monomer molecules can bond directly with one another (condensation cure)5.
Thixotropy
Thixotropy is defined as a reversible behaviour of certain gels that liquefy when they are shaken, stirred, or otherwise disturbed and reset after being allowed to stand. A good example is how Ketchup® from a bottle, exhibits a stable form at rest, but becomes fluid when agitated.
As used with ear impression material, thixotropy allows the material inserted into the ear canal to flow easily, and then to “hold” its position without “sagging” or “flowing” out/from the ear. This is especially important when an impression is made with the head in a vertical position. This issue became a significant consideration as ear impression material was formulated to have low viscosity, featured with silicone material, and even more-so with the easily flowing material used with the gun injection procedure. In the case of ear impression material, the reformation of the silicone is from a semi-liquid to its hardened, polymerized end result. When it does not sag, it is considered to be have thixotropic properties.
In the case of ear impression material, the thixotropic quality is desirable to allow the material to flow sufficiently into the ear canal to form a uniform layer, then to resist further flow, thereby preventing sagging on a vertical surface.
References
- Young, R.J., and Lovell, P.A. (2011) Introduction to Polymers, Third Edition. CRC Press.
- Bradna, P. (2016). Impression materials, Institute of Medical Biochemistry, 1st Med., Charles University and Institute of Dental Research, Prague, Czech.
- Burgess, J.O. Inside Dentistry, Vol. 1, Issue 1, October, 2005.
- Nolan, M. and Combe, C. (1989). In vitro considerations in the production of dimensionally accurate earmolds. I. The ear impression. Scand Audiol. 19, 35-41.
- Johnson, T. Intro to polymers. undated