The desire to use the ear impression as the final earmold was an early objective of some earmold impression providers. For hearing aid dispensers, to be able to provide instant earmolds from impressions would certainly circumvent many of the problems they encountered with delays in delivery, remakes, distant service calls, cost, etc.
Early instant earmolds from impression materials fell into three types: acrylics, silicones, and synthetic rubber polymers, in order of their chronological introduction.
This post continues the history of the development of ear impression materials from four previous posts on this topic: Ear Impression History, From Teeth to the Ear, Ethyl Methacrylate to Silicone, and last week’s post on ethyl methacrylate to silicone ear impressions.
Early Instant Earmolds Made From the Ear Impression
1950s – ADCOmold hard acrylic instant earmold
In the early 1950s, a hearing aid dispenser by the name of Carl Hoffman founded Acousticon Hearing aids of Denver. He recognized the need to have an earmold that provided an “On-the-Spot” application. The brand name reflected the name of his company, ADCO (short for Acousticon Denver Company). Thirty years later, the company was sold and sold again in 2014 with the emphasis shifting more toward products that empowered customers to communicate freely and effectively without barriers, and now goes under the name ADCO Hearing Products. They no longer show as selling instant earmold material.
1957 – ADCOmold’s first instant mold was made using an acrylic (methacrylate), was patented, and became the first of its kind in the hearing aid industry. This was a hard acrylic earmold fabricated from the ear impression itself1.
1958 – Soft earmold
A soft earmold, made from the ear impression, was introduced to the market by Adcomold a year after they introduced their hard acrylic instant earmold1.
1969 – Soft polymer instant earmold
In 1969, a polymer ear impression/earmold material was introduced, resulting from a cooperative effort between Dow Corning Corporation (Frisch) and Zenith Hearing Aid Sales Corporation (Blanchard)2. This was an instant silicone rubber earmold, called Silastic®. This was a semi-liquid polymer mix, that when blended with catalysts, vulcanized to a soft silicone rubber (polydimethylsiloxane rubber, which was Dow Chemical’s original silicone) at room or body temperature in a matter of minutes (essentially the same material introduced by Lloyds3). Unfortunately, as a liquid silicone rubber mix poured into the ear, Silastic tended to trap air bubbles. Frisch and Blanchard had the mixture modified to be used as a non-slump grease-consistency silicone polymer blend, designed to be put into the ear with a dental syringe (Figure 1). The polymer was provided in a metal tube, and the catalytic agents in sealed glass ampules. Interestingly, this author discarded about 75 of these kits just this past summer.

Figure 1. The instant earmold kit designed by Zenith following its introduction by Frisch and Blanchard. It contains pre-measured tubes of Silastic® Brand Earmold Polymer, sealed glass ampules of pre-measured liquid catalysts, syringe, and syringe cleaning brush, mixing spatula, mixing pad, and core drill. After removal, the earmold is trimmed of excess material, and a hole is hand drilled for the eventual tubing. The edges are smoothed with an emery board or small hand grinder. The sound tube is then inserted into the drilled hole. (Image modified by Staab from Zenith Earmold Catalog, undated4).
Of interest with this development was that the material was non-slumping and non-flowing after placement in the ear. This allowed the person being fitted to remain upright, and for both ears to be fitted simultaneously. This may have been the first real attempt at designing ear impression material that was thixotropic (holding its shape during the curing process and not flowing from the ear canal).
In this form, the impression could become the completed earmold, although it never achieved great success for a variety of reasons, including the difficulty of providing a good mechanical connection of the silicone with the nubs of external receivers used with many hearing aids at the time of its introduction5. Still, it continued in the Zenith line at least up to the time when behind-the-ear (BTE) hearing aids no longer used button receivers, but used tubing to carry the sound to the earmold in the ear.
However, it did not take long for this material to be used as noise plugs and swim molds, and modifications of this material continue to be used currently for this purpose.
The silicone rubber material (Silastic® brand from Dow Chemical) was later marketed by Hozer under the Oto-Cure brand name, and marketed from around 1969 at least up to 19746.* It was in the same material as used by Zenith, with one tube containing a soft paste silicon that cured or vulcanized to silicone rubber when mixed with two different catalysts furnished in glass ampules broken open with fingers. Catalyst #1 was used to mix with the silicone, and catalyst #2 was used later (mixed with silicone), to smooth the earmold. This was syringe injected into the ear canal. The company, Oto-Cure Earmolds, Inc. seems to have vanished from the hearing aid ear impression/instant earmold scene.
A Re-emphasis on Instant Earmolds – But For Other Purposes
Recall that in the late 1950s, ADCOmold introduced both hard acrylic and soft earmolds using its impression material. For reasons only speculated, this was not widely adopted by hearing aid dispensers for coupling hearing aids to the ear. This could easily be attributed to the fact that earmold laboratories at that time were able to provide a wide range of earmolds (styles, materials, finished quality) that were difficult to duplicate using material that ended up as the earmold itself. Additionally, the time and skill level involved were beyond many dispensers. This seems to be confirmed by A.G. Babington in 1975 when asked if he had been working on attempts to make instant earmolds7. His response:
“No, I haven’t. There is a need for instant earmolds, it is for instance a good idea, if the patient is tested with a proper fitting earmould, also when the patient cannot go to the hospital, but you have to examine him in his home. Up till now they have limitations they do not look nice, and the life is not very long. I think they have a limited use.”
In spite of such comments and attitudes, instant earmolds found a new and expanded market as swim plugs and noise protectors, as mentioned earlier. For this purpose, instant earmolds worked well, and expanded the market by involving many individuals outside of the hearing health care professional community.
1970 – Insta-Mold
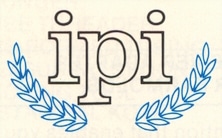
Insta-Mold Prosthetics, Inc.
Insta-Mold was established in 1970 by Sydney M. Gurschkov, Ph.D., who combined his chemistry background with his experience as a certified hearing aid dispenser8. Gurschkov introduced his product, a synthetic rubber polymer, as Insta-Mold. He packaged the polymer in a jar as a soft, dough-like consistency. With this came a skin texture heavy liquid in an eye dropper bottle that acted as a hardener (catalyst) by just applying the proper number of drops to the “Insta-Mold mix.” Application could be by hand pack or syringe method.
Insta-Mold has claimed to be the first elastic rubber silicone to be used by kneading to shape earmolds and earplugs. In this process, the impression became the earmold or earplug. Another claim was that the polymers used were pure silicone, and did not use filler, the latter reducing the silicone content and resulting in a poorer ear impression.
The Insta-mold processes led also to:
- Instant Silicone Swim plugs
Kasden and Robinson9 used high-viscosity silicone polymer from Insta-Mold to produce swim plugs that were nontoxic, nonallergenic, nonshrinkable, and very soft. A hand packing technique was used.
- Insta-Seal silicone earmold for impedance and clinical hearing aid evaluations.
These were made as a temporary seal of the ear to complete a required evaluation. These were not to be confused with permanent non-shrinkable type silicones such as Insta-Mold Swimmold, Earmold, or Noise Protectors. The reason was because the Insta-Seal silicone used for these temporary earmolds contained oils other than silicone which migrated out of the product and led to eventual shrinkage. It is assumed that a lower grade silicone (or filler added) was used to make this cost effective for temporary earmolds.
- Instant earmold with receiver adapter rings for silicone earmolds (Insta-mold).
These were made at least since 1977. A regular Insta-Mold earmold was made, but before it had cured, an adapter ring was pressed into the earmold. After the earmold had cured, this was followed immediately with an application of Insta-Seal Kote (sealer). After the surface dried, an opening was bored through the adapter ring and out through the tip that entered the ear canal. A snap ring was used to connect an external receiver (for body aids, auditory trainers, stethoscopes, radio headsets, telephone headsets, many one- and two-way radio and paging systems). The kit is shown in Figure 2.
The information on Insta-Mold products is taken from their publications, none of which are dated10,11,12,13,14,15.
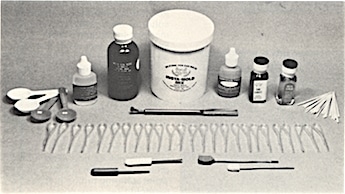
Figure 2. Insta-mold kit containing everything to make an on-the-spot earmold. Insta-mold mix, hardener paste, hand lotion, insta-cement, applicators, core drill, plunger, tube threader, pre-formed tubing, measuring spoons, packing tool, instal-seal Kote.
1975 – Dura-flex polymerized vinyl compound
Most of the ear impression material used up through 1975 consisted of powder and liquid (ethyl methacrylate monomer-polymer). However, a Dura-flex polymerized vinyl compound was made specifically for Phonic Ear16. This had a rubber-like texture promoted to hold its shape indefinitely, being extremely tough, pliable, and which could not be broken or “chewed.” It is suspected that the latter advantage resulted from the fact that Phonic Ear’s hearing aids were fitted primarily to children at that time.
1979 – Audi-Sil Silicone
The Audiplast Products/Division of Coe Laboratories introduced Audalin, and then later Audi-Sil Silicone impression material (Figure 3) to make quick and easy earmolds, attenuators, and ear plugs for swimmers17. Coe was acquired by GC Dental Industrial Corporation in 1990, and discontinued ear impression material, seemingly to have sold it off to Esschem, who trademarked the Audi-Sil and other names in 1985.
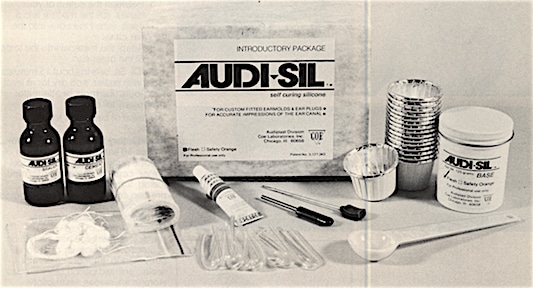
Figure 3. Audi-sil instant earmold material. The kit contains enough for 16 ear molds. It includes a jar of silicone putty, scoop, tube of accelerator, cement, sealer, pre-formed tubing, tube puller, earmold drill, pre-tied cotton blocks, cups, storage envelopes, and instructions.
*This information is from notes by Wayne Staab, but there is no reference or year date. The Oto-Cure Earmolds “Instructions for Earmolds and Holders” provides photos and information about the impression material. By all indications, this is the same instant earmold material from Dow Chemical as used by Frisch and Blanchard in 1969.
References
- Berger, K.W. The Hearing Aid: Its Operation and Development, 1974 Revised Edition, p. 117, National Hearing Aid Society, Livonia, Michigan.
- Frisch, E.E., and Blanchard, F.J. Instant silicone rubber earmolds. National Hearing Aid Journal, Dec. 1969, pp 8-9.
- Instructions for Lloyd’s mixture ear impression material. Published by Royal Industries, Audiotone Division, Phoenix, Arizona, USA.
- Zenith Earmold Catalog, Zenith Hearing Aid Sales Corporation, HA-55, Chicago, IL, undated.
- Davis, H., and Silverman, R. Hearing and Deafness. (1970). Holt, Rinehart & Winston, Inc. New York. 296.
- Konkle, D.F., and Bess, F.H. Custom earmolds in hearing aid evaluations, Maico Audiological Library Series, Vol. XII, Report Five. (Author statement: The authors wish to acknowledge Oto Cure Earmolds Inc. for their assistance in supplying the earmold materials).
- Babington, A.G. (1975). Technology of the individual earmould, in Earmoulds and Associated Problems, Dalsgaard, S.G. (Ed.) Scandinavian Audiology Supplementum 5, 63, GL. Avernaes, Denmark.
- https://www.instamold.com/about/
- Kasden, S.D., and Robinson, M.R. (1974). Fabrication of custom-made ear plugs for swimming. Archives of Otolaryngology, July, Vol. 100, p. 68.
- Insta-Mold, the most perfect permanently elastic earmold in minutes, inserted into the ear by hand or syringe. Insta-Mold Prosthetics, Inc., Philadelphia, PA.
- The Insta-Mold process customized earmold that can be made in your office or clinic in minutes. Insta-Mold Prosthetics, Inc., Philadelphia, PA.
- The Insta-Mold process customized swim mold. Insta-Mold Prosthetics, Inc., Philadelphia, PA.
- At last! Custom fitted hearing protection for noise correction with “Insta-Mold” noise guards. Insta-Mold Prosthetics, Inc., Philadelphia, PA.
- Introducing receiver adapter rings for silicone earmolds by Insta-Mold. Insta-Mold Prosthetics, Inc., Philadelphia, PA.
- New! Insta-seal silicone for impedance and clinical hearing aid evaluations. Insta-Mold Prosthetics, Inc., Philadelphia, PA.
- Phonic Ear, Earmolds. 1972. Earmold booklet.
- Audi-Sil Silicone. Description flyer. Coe Audiplast Products/Division of Coe Laboratories.